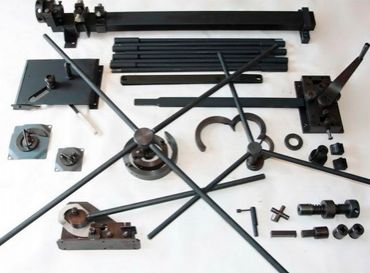
Холодная ковка это – современная технология изготовления металлических изделий. Изделия из холодной ковки изготавливаются из листового или сортового металла.
Что из себя представляет холодная ковка
Холодная ковка – это метод металлообработки, позволяющий создавать декоративные композиции без нагрева металла. Материалу задается определенная форма с помощью механической обработки.
Технология позволяет полностью автоматизировать процесс изготовления изделий. С помощью электросварки создаются декоративные элементы, имеющие высокую прочность, практическую функцию и привлекательный внешний вид.
Какие изделия можно делать с помощью холодной ковки
Используя метод холодной ковки, можно создать крупные и мелкие детали. Изготавливаются спирали, кольца, пики, закрученные прутья и многое другое. Мелкие элементы объединяются в полноценные композиции.
Художественная ковка применяется при изготовлении таких изделий, как:
- решетки и ограды;
- перила для уличных и домашних лестниц, крыльца и мостиков через небольшие водоемы;
- козырьки и навесы;
- фонари и светильники;
- скамейки и беседки;
- садовая и домашняя мебель (стулья, столы);
- ограждения для лоджий и балконов;
- мангалы и каминные решетки;
- предметы декора (вешалки, карнизы, подставки для горшков с растениями, вазы).
Крупные изделия состоят из множества мелких деталей. С помощью данной технологии изготавливаются элементы разных стилей: цветочные композиции, строгая и необычная геометрия, абстракция. Дизайны универсальны, они хорошо смотрятся в любом интерьере и уличной обстановке.
Таким типом формовки можно изготовить различные детали:
- завиток – самый популярный элемент, может иметь форму S и С (волюта);
- спираль – плоская или пространственная, одинарная или двойная;
- крутень – прут или полоска, скрученная вокруг своей продольной оси;
- пика – прут с заостренным наконечником;
- чеканка – тонкий и плоский элемент, часто имитирует листья, цветочные лепестки, цветы и животных;
- кольцо.
При составлении готовой композиции, все детали раскладываются на ровной поверхности и соединяются сваркой или художественными хомутами. Второй способ используется тогда, когда сварочный шов на этом же месте будет слишком заметным. Художественные хомуты дополняют узор и выглядят органично в любой композиции.
Когда сварочные швы остывают, удаляется шлак, и поверхность выравнивается шлифовальной машинкой. Если композиция будет покрашена, болгаркой обрабатывается вся конструкция.
Чем отличается от горячей: плюсы и минусы
Горячая ковка
Воздействие высоких температур повышает пластичность и изменяет характеристики материала. Это главное преимущество технологии.
Горячая ковка подразумевает предварительный нагрев металлических заготовок перед их обработкой. На это уходит много времени и энергии, что увеличивает денежные затраты производства.
Горячей ковкой может заниматься только профессиональный кузнец, прошедший обучение, и знающий сложности процесса. При соблюдении всех технических стандартов и норм, изделия выглядят не хуже предметов, сделанных по горячей технологии. Мебель и декоративные элементы смотрятся дорого и благородно.
У кузнеца гораздо меньше возможностей проявить фантазию. Нагрев материала накладывает строгие ограничения на производство. Для работы требуется кузнечный горн и большие объемы топлива.
Для горячей ковки берется сталь, в составе которой содержание углерода составляет 0,08-0,085%. Она хорошо поддается нагреву, но не подходит для сварки. Материал с содержанием углерода 0,6-1,35% необходимо нагревать перед ковкой и во время обработки.
Холодная ковка
Метод доступен для всех желающих. Можно изготавливать качественные конструкции в домашних условиях. Покупка профессионального дорогостоящего оборудования и получение образования не требуется. Можно собрать станок своими руками.
Изготовление предметов данной технологии гораздо быстрее, чем при горячей ковке. Экономия объясняется отсутствием нагрева металла, на что и уходит большая часть времени. Например, на изготовление одинаковых ворот с помощью формовки уйдет 12 часов, а, если использовать горячую технологию, придется ждать около недели.
Так как в процессе изготовления нет нагревательных устройств, холодная ковка является более безопасной технологией.
Для холодной ковки подходят следующие металлы:
- сталь – сплав железа и углерода (не более 2%);
- алюминий – пластичный материал, который легко поддается изменению формы;
- медь – мягкий металл;
- бронза – сплав меди и олова, подходящий для художественной ковки;
- мельхиор – сплав никеля и меди, устойчивый к воздействию факторов.
В процессе сварки не меняется структура и свойства металла, как при нагреве. Формовка увеличивает прочность металла. Конструкции выдерживают сильные повреждения и удары, что делает их более долговечными.
С помощью технологии можно создать абсолютно одинаковые элементы для общей композиции. Риск брака и деформации в процессе производства минимален.
Самый главный недостаток формовки – ограниченность в выборе исходных форм. Одинаковые детали можно комбинировать, чтобы получить уникальную конструкцию, но количество основ для этого мало. У горячей ковки гораздо больше заготовок, из которых будут созданы полноценные изделия.
Другой минус– потребность в специальном оборудовании. Да, станок и заготовки можно сделать своими руками, но это под силу только профессионалам, новичок не справится самостоятельно.
Так как структура металла не изменяется, необходимо прикладывать больше усилий, чтобы получить нужную форму. В процессе сопротивление поверхностного слоя усиливается жесткостью. Сердцевина материала поддается формированию, только когда преодолевается сопротивление внешних слоев.
Приемы холодной ковки
Главным процессом является создание определенной формы из заготовки. При создании изделий используются следующие типы обработки:
- штамповка;
- ковка;
- гибка;
- скручивание;
- прокат;
- протяжка;
- чеканка.
Выбор технологии зависит от формы и типа металлопроката. Скручивание применяется для прутьев с квадратным сечением. Для работы потребуются тиски и ворот с длинным рычагом. В итоге получается закрученный вокруг собственной оси прут. Иногда в тиски сразу устанавливается 2 изделия. При закручивании они обвивают друг друга.
Для гибки заготовки устанавливается оправка, а конец надежно фиксируется. Материал сгибается и охватывает оправку. Таким способом можно создать завиток или вензель любого размера и формы.
Во время протяжки заготовка перемещается между роликами, которые ее сдавливают. Так, прутьям задается заостренная форма.
Изделия холодной ковки принадлежат разным направлениям. Можно реализовать такие стили, как:
- романс – строгость линий, однотипность деталей и строгая симметрия;
- готика – множество элементов, направленных вверх, раздвоенные спирали и завитки;
- ренессанс – круглые и плавные линии;
- барокко – пышные и ажурные орнаменты, растительные узоры;
- ампир – множество длинных гладких прутьев, вытянутые завитки со спиралями на концах.
Работа начинается с составления чертежа. На нескольких страницах подробно рисуется будущая композиция, берется несколько ракурсов. Лучше чертить в масштабе 1:1, чтобы при создании конструкции не было проблем с размерами и формами.
Оборудование, применяемое при холодной ковке
Холодная ковка из профтрубы выполняется с использованием нескольких типовых устройств.
С помощью «улитки» заготовки завиваются в плоскую спираль. Самый простой способ установки станка – закрепить стальной толстый шаблон к массивному столу. Более сложный вариант представляет собой конструкцию из нескольких звенев, скрепленных шарнирами, которая установлена на вращающемся основании. Заготовку прижимает ролик. Когда вал вращается, шаблон медленно разгибается.
«Гнутик» предназначен для изгиба заготовки под определенным углом. Приспособление состоит из нескольких деталей:
- станина;
- неподвижные упоры с прижимными роликами, обеспечивающими фиксацию заготовки;
- направляющие;
- подвижный упор, перемещающийся по направляющим;
- винтовой механизм.
На подвижный упор устанавливается накладка с профилем, который соответствует нужной форме изгиба. Винтовой механизм создает требуемое усилие. Когда стол поворачивается с закрепленной заготовкой, получается плоская или пространственная фигура любой формы.
На «волне» изготавливаются скругленные зигзаги. Станок состоит из центрального и обводного ролика. Последний монтируется на водиле. «Волну» можно сделать своими руками из «улитки» или «гнутика», установив подвижный упор определенного профиля.
«Фонарик» – это станок, который скручивает несколько стержней одновременно. Элементы устанавливаются по кругу. Результат – пространственная фигура цилиндрической формы со спиральными стенками. Упор с фиксатором и подвижный ворот установлен на станине.
С помощью «глобуса» создаются арочные перекрытие и детали в виде дуг с большими радиусами. Заготовка обжимается по чертежу гибочным рычагом, который двигается с помощью ролика. «Глобус» используется для массового производства одинаковых деталей. Для одного элемента можно использовать «гнутик».
«Твистер» закручивает заготовку по продольной оси. Один конец детали плотно прижимается, а другой вращается с помощью подвижного ворота. Шаг спирали регулируется, так как узел перемещается вдоль всей заготовки.
Это типовые станки, которые используются для изготовления изделий из холодной ковки. Их можно приобрести в профессиональном магазине в Москве. Цены на оборудование не завышены, благодаря чему ковкой может заняться любой желающий.
Изготовление оборудования своими руками
Многие профессиональные мастера работают на самодельных станках. Для создания собственного оборудования достаточно иметь в арсенале шлифовальную машинку и сварочный инвертор.
Станки для холодной ковки нельзя изготавливать из обычной стали. Шаблоны не прослужат долго. Максимальный срок службы такого оборудования составит не больше 1000 рабочих циклов. Для холодной сварки лучше всего подходит инструментальная и конструкционная сталь. Срок службы станков будет в 4-5 раз больше, а готовые изделия получатся с идеальными формами.
Многие устройства имеют пуасоны с разными размерами, но равной формой. Создавать для всех типоразмеров собственное оборудование – лишняя трата денег и времени. Лучше на стадии проектирования станка (для этого подходит «гнутик» или «улитка») предусмотреть возможность смены пуасонов.
Ковка из профильного металла, создание квадратов и прутьев требует больших физических усилий, чтобы получилась идеальная форма. Проблема решается установкой электропривода. Опытные мастера кузнечного дела используют шестеренчатый редуктор.
Оборудование, созданное своими руками, подходит для выполнения разовых работ. Также, самостоятельно сделать станки рекомендуется новичкам, чтобы освоить азы. Когда накопится опыт, можно переходить на профессиональные приборы.
Готовая аппаратура предназначена для серийного производства кованых изделий. Оборудование, созданное в заводских условиях, лучше справляется с большими объемами работы. Получаются более правильные и симметричные формы. Риск получения бракованных деталей минимален.
Холодная сварка – это современная технология изготовления металлических конструкций и художественных изделий. Метод имеет массу преимуществ перед горячим способом, главным из которых является более высокая прочность конечного результата.
Освоить холодную сварку сможет даже новичок. Достаточно изучить базовые вещи и много практиковаться. Лучшим решением будет обучение у профессионального мастера. Он научит работать на специальном оборудовании и создавать оригинальные композиции из металла.